در این مطلب قصد داریم به بررسی نوعی از فولاد بپردازیم که در مقابل زنگزدگی مقاوم است. به این نوع از فولاد، فولاد زنگ نزن یا استنلس استیل میگویند. فولاد زنگ نزن گروهی از آلیاژهای ویژه است که به منظور افزایش مقاومت در برابر زنگزدگی معرفی شدهاند. از ویژگیهای مهم این محصول فولادی میتوان به مقاومت بالا در برابر اکسید شدن، پوسته شدن و تغییر شکل در دماهای بالا اشاره کرد. در این مطلب قصد داریم به بررسی این محصول و انواع آن بپردازیم، با ما همراه باشید.
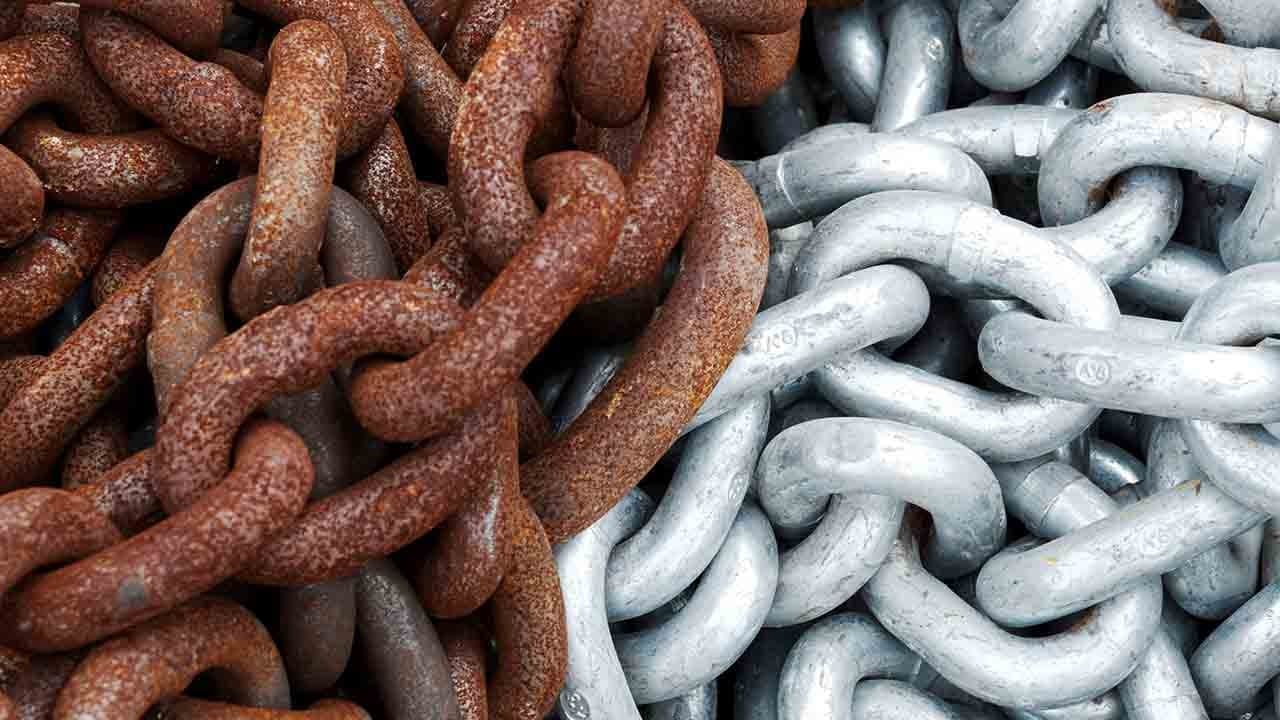
فولاد زنگ نزن چیست؟
فولاد ضدزنگ (آهن زنگ نزن ) یا به اصطلاح استنلس استیل در ترکیب خود مقدار زیادی کروم دارد. حداقل کروم مصرفی در فولاد ضدزنگ حدود ۱۱ درصد است. این کروم به فولاد ساده خاصیت مقاومت در برابر خوردگی میدهد. این فلز با افزودن عناصر دیگر مانند مولیبدن، نیکل و ازت مقاومت خود را در برابر خوردگی و همچنین مقاومت در برابر حرارت را افزایش میدهد. برای اینکه این نوع از فولاد بتواند در برابر زنگزدگی از خود واکنش نشان دهد و به خوبی عمل نماید، نباید میزان کروم استفاده شده در آن از این مقدار کمتر باشد. زیرا وجود همین مقدار از کروم در فولاد باعث ایجاد خاصیت ضدزنگ میگردد. به عبارت سادهتر کروم عنصری میباشد که تقویتکننده مقاومت فولاد در برابر زنگ زدگی است.
به فولاد ضد زنگ اصطلاحا استنلس استیل میگویند.
علاوه بر کروم از ترکیبات دیگری به منظور تولید فولاد ضدزنگ نیز استفاده
1- ساختار متالورژی
خواص آهن زنگ نزن
مقاومت در برابر خوردگی: کروم عنصر آلیاژی است که به استنلس استیل ویژگی مقاومت در برابر خوردگی را میبخشد. گریدهای پایین این آلیاژ در برابر آب و هوا و محیط های خورنده مقاومت میکنند و گریدهای آلیاژی بالا نیز میتوانند در برابر خوردگی در اکثر اسیدها، محلولهای قلیایی و محیطهایدر دنیای امروز به علت پیشرفت صنایع مختلف و کاربرد روز افزون قطعات فلزی، انواع مختلف آهن به ویژه آهن زنگ نزن دارای اهمیت بسیار بوده و به شدت مورد استفاده و توجه هستند. در کشور ما نیز ، بسیار مهم و کاربردی هستند. دلیل استفاده گسترده از انواع آهن زنگ نزن، ویژگیهای خاص، مفید و کاربردی آن ها است که از جمله مهم ترین این خواص مقاوم بودن آن ها در برابر خوردگی یا همان ضد زنگ بودن هست.
همان طور که به طور مختصر اشاره شد، آهن زنگ نزن نامی عمومی برای تعدادی از آهنهای مختلف است که عمدتاً به دلیل مقاومت آنها در برابر خوردگی از آنها استفاده میشود. یکی از محصولاتی که با جنس آهن زنگ نزن به طور گسترده در صنعت تاسیسات مورد استفاده است و در واقع جزء اصلی اکثر صنایع است، لوله های آهنی زنگ نزن هستند. لوله ها به طور کلی از روش های مختلفی دسته بندی می شوند. از مهم ترین خصوصیات لوله ها برای دسته بندی، میتوان به و جنس لوله اشاره کرد.
لوله ها و قطعات مورد استفاده و کاربردی در صنایع مختلف از جنس های مختلفی ساخته می شوند. در میان فلزات پر کاربرد در ساخت قطعات، میتوان به انواع آهن زنگ نزن اشاره کرد. و استیل در بازار موجود بوده و تقاضای بالایی در بازار دارند و در کنار دیگر قطعات با این جنس، یکی از پر استفاده ترین محصولات هستند. برای استفاده درست و مناسب از انواع لوله ها، اتصالات و قطعات مختلف در تاسیسات و صنایع متفاوت ابتدا لازم است تا با خصوصیات جنس آن ها آشنا شویم.
در این مطلب، ابتدا به معرفی آهن زنگ نزن می پردازیم و اقدام به تعریف آن کرده و با ویژگی های فلز آهن و آهن زنگ نزن آشنا خواهیم شد. سپس پس از معرفی ویژگی ها و خصوصیات آهن زنگ نزن، انواع آهن زنگ نزن را بر میشماریم و به آشنایی با مزایا و معایب و همچنین کاربردهای آهن های زنگ نزن می پردازیم. در این بین درباره تاریخچه ای از آهن زنگ نزن و مخترع آن نیز مطالبی را خواهید دید.
آهن زنگ نزن چیست؟
آهن زنگ نزن نام عمومی برای تعدادی از آهنهای مختلف است که عمدتا به دلیل مقاومت آنها در برابر خوردگی از آنها استفاده میشود. تمامی آهنهای زنگ نزن دارای حداقل ۱۰.۵ درصد کروم هستند. این عنصر با اکسیژن موجود در هوا واکنش میدهد و یک لایه سطحی کروم اکسید پیچیده ایجاد میکند که نامرئی است، اما برای جلوگیری از ترکیب بیشتر اکسیژن و پیشگیری از زنگ زدن سطح کفایت میکند.
تاریخچه آهن
آهن با نماد شیمیایی Fe، نام یک عنصر شیمیایی با عدد اتمی ۲۶ و چگالی ۷۸۷۴ کیلوگرم بر مترمکعب است. آهن یک فلز است و از دیدگاه جرم، بزرگترین عنصر سازنده کره زمین است. آهن اصلیترین عنصر سازنده هسته بیرونی و درونی زمین و چهارمین عنصر متداول در پوسته است. این امر حاکی از فراوانی آن در زمین بوده و امکان به کارگیری آن برای ساخت قطعات مختلف را نشان می دهد. در ادامه نگاهی به تاریخچه استفاده از آهن و پس از آن آهن زنگ نزن در زمین می اندازیم.
ورق st52 با نام فولاد 1.0570 نیز شناخته می شود و در دسته فولاد های کم آلیاژ قرار دارد.
اولین آهن شکل گرفته که توسط بشر در دوره پیش از تاریخ مصرف شد از شهاب سنگ ها آمده بود. ذوب آهن در کوره ها در هزاره دوم پیش از میلاد شروع شد، آثار کشف شده از آهن ذوب شده از ۱۲۰۰–۱۸۰۰ پیش از میلاد در هند و در مشرق از حدود ۱۵۰۰ سال پیش از میلاد بدست آمده است. در حدود 1۴۰۰ پیش از میلاد، از قطعات آهنی در قلمرو هیتیها در ارمنستان کنونی استفاده میشد که این به عنوان نخستین نمونه های مشاهده شده از مصرف این عنصر است.روند شکل گیری و اختراع آهن زنگ نزن به شرح زیر است.
تاریخچه آهن زنگ نزن
پیر بارتبه مهندس فرانسوی در سال ۱۸۲۱، مشاهده کرد که با افزایش مقدار مشخصی کروم به آهن، سفتی و مقاومت به خوردگی اسیدی آن بسیار افزایش مییابد. در ۱۹۰۹، لئون گویله و آلبرت پورتوین بهطور مستقل در فرانسه ریزساختار آلیاژهای Fe-Cr و Fe-Cr-Ni را بررسی کردند. در ۱۹۱۳ هری بریرلی متالوژیست انگلیسی برای اولین بار، با صنعتی سازی فولاد مارتنزیتی، این کشف را تجاری سازی کرد. عده ای به همین علت هری بریرلی را مخترع آهن زنگ نزن می داند. در زیر تصویر او را مشاهده می کنید.
آهن زنگ نزن یکی از پرکابردترین فولادهایی است که در صنایع مختلف از آن استفاده میشود و نقش مهمی در زندگی روزمره انسان دارد. همانطور که از نام آن پیداست این آهن، ضد زنگ است و دچار خوردگی نمیشود. فرآیند زنگ زدن به اکسیداسیون آهن گفته می شود که عموما به واسه واکنش با اکسیژن انجام می شود ولی نمونه های دیگری از زنگ زدن وجود داشته که از واکنش آهن و کلر حاصل می شوند که با نام زنگ سبز شناخته می شود. آهن زنگ نزن به علت دارا بودن حداقل ۱۰.۵ درصد کروم، دچار زنگ زدگی نمی شود.
یکی از رایج ترین ترکیب های که وجود دارد زنگ است که از ترکیب اکسید آهن هست. آهن در این ترکیب خیلی سریع با اکسیژن ترکیب می شود و زنگ آهن را پدید می آورد. در طبیعت خیلی کم می توان آهنی را یافت که خالص باشد.
به طور خلاصه تعریف آهن زنگ نزن به شرح زیر است:
آهن زنگ نزن در اصل اصطلاح درست فولاد زنگ نزن است. زیرا هنگامی که کربن به آهن افزوده می شود تبدیل به آلیاژ تبدیل شده و از وضعیت عنصری خود خارج می گردد. این آلیاژ ضد زنگ بوده و به راحتی دچار خوردگی نمی شود. به علت فعال بودن فلز آهن وقتی در مجاورت اکسیژن و رطوبت قرار می گیرد به اصطلاح می گویند زنگ زده است، در واقع آهن با اکسیژن تشکیل اکسید آهن داده که قرمز رنگ بوده و روی آن را می پوشاند.
در این بخش با تعریف آهن زنگ نزن و یکی از خصوصیات بارز آن که ضد زنگ و خوردگی بودن آن است، آشنا شدیم همچنین به طور خلاصه به تاریخچه آهن و آهن زنگ نزن اشاره کردیم. در بخش بعدی به ویژگی های مختلف آهن زنگ نزن می پردازیم.
ویژگی های آهن زنگ نزن
همان طور که پیشتر، آهن زنگ نزن را تعریف کردیم، می دانیم که آهن زنگ نزن (فولاد زنگ نزن) در واقع آلیاژی از آهن است که اصلیترین عناصر تشکیل دهنده آن آهن، کروم و نیکل است و در آن حداقل درصد جرمی کروم ۱۰٫۵ درصد و حداکثر درصد جرمی کربن ۱٫۲ درصد است.
آهن های ضد زنگ، به دلیل خاصیت غیرفعال شدن خود توانایی مقاومت بسیار خوبی در برابر خوردگی از خود نشان می دهند. آهن های زنگ نزن به دلیل شکل گرفتن یک لایه غیر فعال بر روی سطحشان که به شدت به ماده زیرین پیوند خورده است و از تماس بیشتر ماده به محیط اطراف جلوگیری میکند چنین خاصیتی دارند. برای اینکه این پدیده غیرفعال سازی به طور پایدار در فولاد اتفاق بیفتد نیاز است که حداقل ۱۰٫۵ درصد از ماده را کروم تشکیل دهد.
مهم ترین ویژگی های آهن
- آهن دارای سطح صاف و نقره ای براق مایل به رنگ خاکستری است.
- آهن وقتی در هوا با اکسیژن ترکیب می شود به رنگ قرمز یا قهوه ای در می آید.
- آهن فراوان ترین فلز در شهاب سنگ ها و در هسته فلزی متراکم در سیاراتی مثل زمین است.
- آهن خالص فلز است، اما به ندرت در این شکل روی سطح زمین یافت می شود زیرا در حضور اکسیژن و رطوبت به آسانی اکسیده می شود.
مهم ترین ویژگی های آهن ضد زنگ
- دارای حداقل ۱۰٫۵ درصد از ماده کروم است.
- مقاوم در برابر اکسایش و زنگ زدگی و حمله اسیدها
- سطوح بالاتر کروم و همچنین افزودن سایر عناصر آلیاژی مثل نیکل و مولبیدن لایه سطحی را تقویت کرده و مقاومت آن را در برابر خوردگی مواد ضد زنگ افزایش می دهند.
- کروم همیشه عامل تعیین کننده است، اگرچه عناصر دیگر مثل نیکل و مولبیدن برای افزایش مقاومت در برابر خوردگی استفاده می شوند.
- آهن زنگ نزن به طور کامل قابل بازیافت است.
استفاده از آهن به علت فراوانی آن و آهن زنگ نزن به دلیل همین ویژگی های زنگ نزن بودن و مقاومت بالای آن در برابر خوردگی در ساخت صنایع مختلفی از قبیل ساختمان سازی، سازههای زیرساختی، ابزارها، کشتیها، قطارها، خودروها و اکثر ماشین آلات و تجهیزات صنعتی، کاربرد گسترده دارد.
در ادامه با شیوه تولید آهن و آهن زنگ نزن آشنا می شویم.
تولید آهن فلزی و آهن زنگ نزن
برای ساخت آهن، دو روش عمده وجود دارد. روش اول آزمایشگاهی و روش دوم صنعتی است. روش اول به منظور تولید آهن خالص است. در ادامه این دو روش شرح داده شده اند.
در برخی کاربردهای خاص که به آهن خالص نیاز است میتوان آن را در آزمایشگاه در مقادیر کم از طریق کاهش اکسید خالص یا هیدروکسید آن با هیدروژن تولید کرد، یا میتوان پنتاکربونیل آهن را تا ۲۵۰ درجه سلسیوس گرم کرد تا تجزیه شده و آهن خالص پودری ایجاد گردد. روش دیگر الکترولیز کلرید آهن بر روی کاتد آهنی است.
امروزه، تولید صنعتی آهن، آهن زنگ نزن یا فولاد از دو مرحله اصلی تشکیل شده است. در مرحله اول، سنگ آهن با کک در کوره بلند کاهش یافته و فلز مذاب از ناخالصی هایی مانند کانیهای سیلیکات جدا می شود. در این مرحله آلیاژی به نام آهن خام تولید می شود که حاوی مقادیر نسبتاً زیادی کربن است. در مرحله دوم، توسط فرایند اکسایش مقدار کربن موجود در آهن خام کاهش مییابد تا آهن فرفورژه، فولاد یا چدن تولید شود. در این مرحله میتوان سایر فلزات را برای ساخت آلیاژهای فولادی به آن اضافه کرد.
انواع آهن زنگ نزن
در این بخش انواع آهن زنگ نزن بررسی و معرفی شده اند. سه دسته اصلی انواع آهن زنگ نزن و ویژگیهای آنها به شرح زیر است:
- آلیاژهای کروم، نیکل و آهن با کروم ۱۶ تا ۲۶ درصد، نیکل 6 تا 26 درصد و مقدار کمی کربن با خواص غیر مغناطیسی.
- نیکل مقاومت در برابر خوردگی را افزایش میدهد.
- سخت شدن آن در دمای پایین و همچنین زمانی که گرم شود و بعد خنک شود است.
- نوع ۳۰۴ یا S۳۰۴۰۰ یا 1۸/۸ (۱۸ درصد کروم، ۸ درصد نیکل) پر استفادهترین ترکیب است.
- آلیاژهای کروم- آهن با ۱۰.۵ تا ۱۷ درصد کروم و ترکیبات کربن به دقت کنترل شده است.
- سخت شدن آن به وسیله خنک شدن (به سرعت در آب یا روغن خنک میشود) و تغییر دما (گرم میشود سپس خنک میشود) است.
- مارتنستیک خواص مغناطیسی دارد.
- عمدتا در ساخت چاقو استفاده میشود.
- درجات مارتنستیک قوی و سخت هستند و شکل دهی و جوش کردن آنها سخت و دشوار است. نوع ۴۲۰ (S۴۲۰۰۰) نمونه معمول آن است.
- آلیاژهای کروم- آهن با ۱۷ تا ۲۷ درصد کروم و با مقدار کمی کربن و دارای خواص مغناطیسی است.
- ظروف آشپزی ساخته شده از این نوع حاوی سطوح بالاتر کروم است.
- نوع ۴۳۰ رایجترین فریتیک مورد استفاده است.
- دو نوع دیگر آن شامل دوپلکس (با ساختارهای آستنیتیکی و فریتیکی) و رسوبات سخت شده آهن ضد زنگ است که در شرایط خاصی استفاده میشود.
علت زنگ نزن بودن آهن زنگ نزن (استنلس استیل) در ادامه آورده شده است:
هنگامی آهن ضد زنگ می شود که در میان عناصرش حداقل 10.5% کروم داشته باشد. این مقدار کروم پس از ترکیب شدن با اکسیژن هوا بر روی آهن زنگ نزن لایه ای را به نام اکسید کروم تشکیل می دهد که این لایه دیده نمی شود. این لایه باعث از بین رفتن ارتباط بین آهن و هوا می شود و در نتیجه آهن سالم می ماند. هر چه قدر مقدار کروم همراه عناصر دیگری همچون نیکل و مولیبدن بیشتر باشد این لایه تقویت می شود و خاصیت ضد زنگ بودن آهن را افزایش می دهد.
اگرچه آهن زنگ نزن نسبت به فولاد معمولی کربن یا دیگر آلیاژها در برابر خوردگی مقاوم تر است، اما در برخی موارد میتواند دچار خوردگی شود. این آهن کمتر زنگ میزند نه اینکه اصلا زنگ نزند. در محیطهای معمولی جو یا آب، آهن زنگ نزن خورده نمیشود و در سینکهای خانگی، سرویسهای غذا خوری، ماهی تابه و سطوح کار استفاده میشود و خوردگی ایجاد نمیکند.در شرایط شدید تر، آهن زنگ نزن اصلی ممکن است دچار خوردگی شود و در این صورت آلیاژ قوی تری از آهن زنگ نزن باید مورد استفاده قرار گیرد.
در ادامه به کاربرد های آهن زنگ نزن اشاره شده است.
مزایا، معایب و کاربرد های آهن های زنگ نزن چیست؟
آهن زنگ نزن یک ماده همه کاره است که می تواند برای طیف گسترده ای از کاربرد های مختلف استفاده شود. این کاربرد بسیار زیاد به علت ویژگی های مناسب آن است. از انواع مختلف آهن زنگ نزن برای ساخت هزاران وسیله استفاده می شود. در زیر به تعدادی از آنها اشاره میکنیم:
- کاربرد خانگی: کارد و چنگال، سینکها، ماهی تابه، گردونه ماشین لباس شویی، کوره ماکروفر، انواع تیغ.
- صنعت نفت و گاز: پایگاههای نفت و گاز در منزل، جعبه کابل، خطوط لوله زیر زمینی.
- پزشکی: تجهیزات جراحی، جراحی ایمپلنت، اسکنر ام آر آی (MRI)
- غذا و نوشیدنی: تجهیزات پذیرایی، جوشاندن، تقطیر، پردازش مواد غذایی.
- آب: آب و فاضلاب، لولههای آب، مخازن آب گرم.
- معماری و مهندسی عمران: روکشها، نرده ساختمان، اتصالات درب و پنجره، مبلمان خیابانی، بخشهای ساختاری، نوار تقویت شده، ستونهای روشنایی، تیر سردرها، پایههای بنایی.
- حمل و نقل: سیستمهای اگزوز، پنجره و داخل خودروها، تانکرهای خیابانی، انبارهای کشتی، تانکرهای کشتی حامل مواد شیمیایی، باقی مانده وسایل نقلیه.
- کاربرد شیمیایی دارویی: مخازن تحت فشار، لولههای فرآیند.
- کاربرد عمومی: فنرها، چفت وبستها (پیچ و مهره و واشرها)، سیم.
همچنین مزایای استفاده از لوله های آهن زنگ نزن که از کاربردی ترین قطعات ساخته شده با جنس آهن ضد زنگ (استینلس استیل) هستند، به شرح زیر است:
- وزن سبک
- با دوام
- مقاومت در برابر خوردگی بالا
- قابل بازیافت و سازگار با محیط زیست
حاوی کلر مقاومت کنند.
مقاومت در برابر آتش و حرارت: گریدهای مخصوص آلیاژی با کروم و نیکل بالا، در برابر پوسته پوسته شدن مقاوم بوده و در دمای بالا استحکام بالای خود را حفظ میکنند.
ظاهر زیبا: سطح روشن فولاد ضد زنگ که به راحتی نگهداری میشود، ظاهر مدرن و جذابی را ارائه میدهد.
نسبت استحکام به وزن: قابلیت سختکاری گریدهای آستنیتی، منجر به تقویت قابل توجه خواصی از این فولاد میشود که امکان دسترسی به چنین سطحی از خواص، در اثر کارسرد وجود نداشت. همچنین گرید داپلکس با استحکام بالا، باعث کاهش ضخامت مواد نسبت به گریدهای معمولی میشود که باعث صرفهجویی قابل توجهی در هزینه میشود.
سهولت ساخت: تکنیکهای مدرن فولادسازی به این معناست که آهن زنگ نزن را میتوان به آسانی مانند فولادهای سنتی جوش داد، خم کرد، شکل داد، ماشین کاری کرد و در انتها مونتاژ کرد و آن را ساخت. جوشکاری انواع فولاد ضد زنگ و روش های آن را مطالعه کنید.
مقاومت در برابر ضربه: گریدهای آستنیتی سری 300، مقاومت بالا را در دمای بالا و بسیار پایینتر از انجماد فراهم میکند و این فولادها را برای کاربردهای دما پایین (دماهای زیر صفر درجه سانتیگراد) مناسب میکند.
صرفه اقتصادی در بلند مدت: با در نظر گرفتن هزینه کل، مناسب است که هزینه مواد و تولید و هزینه چرخه عمر را در نظر بگیریم. وقتی هزینههای کل چرخه عمر در نظر گرفته میشود، آهن زنگ نزن اغلب ارزانترین گزینه است. در واقع این محصول، صرفهجویی در هزینه را بدون تعمیر و نگهداری و با طول عمر طولانی به دست میدهد.
قابل بازیافت: این نوع فولاد قابلیت بازیافت 100 درصدی داشته و بیش از 50% از محصولات جدید، از ضایعات استنلس استیل قدیمی تولید میشوند.
جنبههای بهداشتی: نظافت از اهمیت بالایی برخوردار است. قابلیت تمیز کردن آسان استنلس استیل ، آن را به اولین انتخاب برای شرایط سخت بهداشتی مانند بیمارستانها، آشپزخانهها و کارخانههای پردازش غذا تبدیل میکند.
اجزای سازنده فولاد زنگ نزن
فولادهای ضد زنگ شامل تعدادی عنصر آلیاژی با توجه به گرید و ترکیب خاص هستند. در زیر اجزای سازنده آلیاژی آهن زنگ نزن با ذکر دلیل حضور آنها آورده شده است.
نحوه تولید فولاد زنگ نزن
مراحل تولید فولاد ضد زنگ به شرح زیر میباشد:
1- ذوب شدن: مواد اولیه در کوره قوس الکتریکی با هم ذوب میشوند. با اعمال حرارت شدید، 8 تا 12 ساعت طول میکشد تا فلز ذوب شود.
3- تنظیم: اکثر فولادهای ضد زنگ دارای کیفیت دقیق هستند. فرآیند تنظیم اجازه میدهد تا تنظیمات خوبی در ترکیب شیمیایی انجام شود. تنظیم زمانی است که فولاد به آرامی هم زده میشود تا عناصر ناخواسته را از بین ببرد و قوام را بهبود بخشد، در حالی که ترکیب مورد نیاز را در محدوده دما حفظ میکند.
5- نورد گرم: نورد گرم در دمایی بالاتر از دمای تبلور مجدد فولاد انجام میشود. درجه حرارت دقیق بستگی به گرید استنلس استیل مورد نظر دارد. فرم های فولادی گرم میشوند و از غلتکهای بزرگی عبور میکنند. در طی این مرحله، بلومها و بیلتها به میله و سیم تبدیل میشوند. صفحات نیز به صورت ورق و نوار در میآیند.
5- نورد سرد: نورد سرد در مواردی مورد استفاده قرار میگیرد که ابعاد بسیار دقیق یا یک تمامکاری جذاب مورد نیاز است. این فرآیند در زیر دمای تبلور مجدد فولاد اتفاق میافتد. نورد سرد با استفاده از غلتکهای با قطر کوچک و یک سری غلتکهای نگهدارنده انجام میشود. این فرایند امکان تولید ورقهای عریض با سطوح بهبود یافته را فراهم میآورد.
6-پخت: آنیل فرآیندی است که برای نرم کردن استنلس استیل، بهبود شکلپذیری و اصلاح ساختار دانه استفاده میشود. همچنین برای از بین بردن تنشهای داخلی فلز ناشی از پردازش قبلی نیز مورد استفاده قرار میگیرد.
7- رسوب زدایی: فرآیند پخت باعث ایجاد رسوباتی روی فولاد به شکل لکه میشود. این لکهها معمولا از طریق شستوشوی فولاد با محلولهایی که شامل اسید نیتریک- هیدروفلوریک است، پاکسازی میشوند. تمیز کردن الکتریکی یک روش جایگزین است که از جریان الکتریکی برای حذف رسوبات استفاده میکند.
8- برش دادن: فولاد ضد زنگ را میتوان به اندازه دلخواه برش داد. برش مکانیکی رایجترین روش است. آهن زنگ نزن را میتوان مستقیماً با چاقوهای گیوتین، چاقوهای دایرهای و یا با استفاده از تیغههای با سرعت بالا برش داد. روشهای دیگر شامل برش شعله است که از مشعل شعلهورشده با اکسیژن، پروپان و پودر آهن استفاده میکند؛ یا برش جت پلاسما که در آن از ستون گاز یونیزه شده همراه با قوس الکتریکی برای برش فلز استفاده میشود.
9- تمامکاری: پوشش سطح برای محصولات استنلس استیل مهم است؛ به ویژه در مواردی که ظاهر آنها مهم باشد. درحالیکه اکثر مردم با ظاهر آهن زنگ نزن استفاده شده برای محصولات مصرفی آشنا هستند، در واقع تعدادی از گزینه های تکمیلی نیز وجود دارد. معمولاً برای خرد کردن یا صیقل دادن فولاد از چرخهای سنگزنی یا تسمههای ساینده استفاده میشود. روشهای دیگر عبارتند از چرخش پارچهای با ذرات ساینده، حکاکی خشک با استفاده از سندبلاست و اچ مرطوب با استفاده از محلولهای اسیدی. همچنین باید توجه داشت که سطح صاف، مقاومت بهتری در برابر خوردگی ایجاد میکند.
انواع فولاد زنگ نزن
فولادهای ضد زنگ بر حسب نوع ریزساختار آنها به گروههای زیر تقسیم میشود:
آهن زنگ نزن آستنیتی
گروه آستنیتی از متداولترین نوع فولادهای ضد زنگ هستند. فولادهای زنگ نزن آستنیتی، در مقایسه با انواع دیگر، حاوی مقادیر زیادی کروم، مولیبدن و نیکل هستند. آنها بسیار متنوع بوده و به دلیل برخورداری از استحکام و چکش خواری عالی شهرت دارند.
آهن زنگ نزن فریتیی
فولادهای زنگ نزن فریتی حاوی مقدار کروم 5 تا 10 درصد بوده و معمولاً دارای غلظت کربن کمی بیش از 0.1 درصد هستند. فولادهای ضد زنگ فریتی مغناطیسی هستند و در درجه اول به دلیل مقاومت در برابر اکسیداسیون و ترک خوردگی تنشی انتخاب میشوند.
آهن زنگ نزن داپلکس یا دو فازی
، حاوی ریزساختاری از مخلوط آستنیت و فریت میباشد و در نتیجه فلزی قویتر از هر دو ایجاد میکند. این استحکام بالاتر میتواند منجر به کاهش قابل توجه وزن شود. مقاومت عالی آن در برابر خوردگی، حتی در محیطهای سخت، آن را برای استفاده در کاربردهای دریایی مناسب میکند.
آهن زنگ نزن مارتنزیتی
فولاد ضد زنگ مارتنزیتی از نظر ساختاری مشابه فولاد ضد زنگ فریتی بوده اما دارای کربن بالا تا حدود 1.2 درصد است که میتواند تا حد زیادی سخت شود. این دسته به ویژه برای تولید ابزار پزشکی و ابزار جراحی مفید هستند.
آهن زنگ نزن رسوب سخت شونده
فولادهای ضد زنگ PH یا رسوب سخت شونده حدود 17% کروم و 4% نیکل دارند. این فولادها میتوانند از طریق افزودن آلومینیوم، تیتانیوم، نیوبیوم، وانادیوم و یا نیتروژن که باعث ایجاد رسوبات منسجم بین فلزی در طی فرآیند عملیات حرارتی موسوم به رسوبسختی میشوند، مقاومت بسیار بالایی ایجاد کنند. با تشکیل رسوبات منسجم در سراسر ریز ساختار، آنها به شبکه کریستالی فشار میآورند و مانع حرکت نابجاییها یا نقایص در شبکه بلوری میشوند. از آنجا که حرکت نابجاییها اغلب عامل اصلی تغییر فرم پلاستیکی میباشد، این امر باعث سختشدن استنلس استیل میشود.
کاربرد فولاد ضد زنگ
با توجه به خواص آهن زنگ نزن، استفادههای گستردهای از این فلز میشود که شامل بخشهای زیر است:
- تولید وسایل آشپزخانه شامل ظروف غذا، کارد و چنگال
- تولید ابزار پزشکی و ابزار جراحی
- قابل استفاده در محیطهای خورنده و شور
- مبدلهای حرارتی
- دیگهای بخار
- آبگرمکنهای تغذیه
- شیرآلات و خطوط اصلی جریان
- هواپیما و کاربردهای هوافضا
مینمایند. از جمله این ترکیبات میتوان به مولیبدن و نیکل اشاره کرد. نیکل به منظور ایجاد انعطاف و افزایش فرمپذیری در فولاد ضدزنگ مورد استفاده قرار میگیرد. کشف فولاد ضدزنگ به این صورت بود که دانشمندان دریافتند با افزودن حدود ۱۰ الی ۲۰ درصد کروم و نیکل به فولاد موجود، نوعی دیگر از فولاد به دست میآید که در برابر اسیدها و زنگزدگی مقاوم هستند. در زندگی روزمره خود با مواردی روبهرو میشویم که از فولاد تولید شدهاند؛ مانند لوازم برقی، وسایل ماهیگیری و بسیاری دیگر.
این نوع از فولاد براق است و به راحتی صیقل داده میشود. بدین منظور از آهن ضدزنگ به عنوان جایگزینی برای نورافکنها و آینهها استفاده میکنند.
فولاد زنگ نزن نوعی محصول فولادی است که در ترکیب خود دارای مقادیر زیادی کروم بوده و جهت افزایش مقاومت در برابر خوردگی تولید میشود. این محصول در انواع متفاوتی عرضه میشود که هرکدام کاربردهای گستردهای در صنایع مختلف دارند.
انواع فولادهای زنگ نزن
فولادهای ضد زنگ بر مبنای ترکیبات شیمیایی و متالوژیکی، معمولا در پنج کلاس مختلف دستهبندی میشوند:
- مارتنزیتی (Martensitic)
- فریتی (Ferritic)
- آستنیتی (Austenitic)
- آستنیتی- فریتی یا دو فازی (Duplex or ferritic-austenitic)
- رسوب سختی (Precipitation-Hardening or PH)
در ادامه هر کدام را به صورت جداگانه توضیح میدهیم.
این نوع گروهی از آلیاژهای ضد زنگ است که آلیاژ سهگانهای از آهن، کروم و کربن است و ساخته شده تا در برابر خوردگی و عملیات حرارتی مقاوم باشد. تمام گریدهای مارتنزیتی، فولادهای کروم مستقیم بدون نیکل هستند. به عبارت دیگر در این نوع از فولاد ضدزنگ نیکل وجود ندارد و عملیات سختگردانی به صورت حرارتی انجام میشود.
میزان کروم موجود در این فولاد میتواند از ۱۱ تا تا ۱۸ درصد باشد و همچنین مقدار یک درصد نیز کربن دارد. استحکام، سختی و مقاومت در برابر خستگی در این نوع از استنلس استیل (آهن زنگ نزن) بالا است. از نظر انعطافپذیری و استحکام در سطح خوبی قرار دارد، ولی در برابر خوردگی مقاومت متوسطی را داراست؛ به طور کلی نسبت به سایر انواع فولادهای ضد زنگ، از مقاومت کمتری در برابر خوردگی برخوردارند، مغناطیسی بوده و از قابلیت جوش و شکلپذیری پایینی برخوردارند. معمولا برای ساخت شیرآلات، فنرها، قاشق و چنگال از فولاد ضد زنگ مارتنزیتی استفاده میکنند.
فریتی (Ferritic)
به طور کلی فولادهای فریتی مقدار کروم بالاتری نسبت به فولادهای مارتنزیتی دارد و به طور نرمال درصد کروم آن بین ۱۱ تا ۳۰ درصد وزنی است. اما درصد نیکل آن یا خیلی کم است و یا بدون نیکل است. ساختار کریستالی این نوع فولاد Bcc است و این فولادها مغناطیسی بوده اما عملیات حرارتیپذیر نمیباشند. این فولادها عموما در کاربردهای غیرساختاری مورد استفاده قرار میگیرد که نیاز به مقاومت به خوردگی بالایی دارد. فولادهای ضد زنگ فریتی از مقاومت حرارتی و خوردگی خوبی برخوردار هستند اما به طور خاص و ویژهای از مقاومت بالایی در برابر کلراید برخوردار است. گرچه خواص مکانیکی مثل تافنس در دمای پایین و آن نسبت به انواع فولاد ضدزنگ فریتی پایینتر است. از جمله کاربرد این نوع از فولادهای ضد زنگ عبارتند از: اگزوز خودرو، ظروف پخت و پز و لوازم خانگی.
انواع فولاد ضدزنگ آستنیتی حاوی حداقل ۱۶ درصد کروم و سه درصد نیکل هستند. این فولاد زنگ نزن بیشترین میزان استفاده را در بین سایر فولادهای ضدزنگ دارد. حدود ۸۰ درصد فولاد ضد زنگ در بازار جهان به فولاد آستنیتی اختصاص پیدا کرده است. حداقل نیکل مصرفی در این نوع، حدود هفت درصد بوده و همین امر باعث شده تا در دماهای بالا انعطافپذیر و مقاوم باشند. شرایط آن از نظر جوشکاری کاملا مساعد است و در محیطهای مختلف مانند آب دریا و محیطهای اتمسفری کاربرد دارد.
فولاد زنگ نزن انواع مختلفی دارد که باتوجه به کاربرد در صنایع از آن ها استفاده می شود.
تحویل و بارگیری محصولات کارخانجات میلگرد میانه، تیرآهن اصفهان، میلگرد شاهرود و …. همگی در کمترین زمان توسط مرکزآهن امکان پذیر است.
به دلیل مقدار بالای کروم و نیکل، بیشترین مقاومت در برابر خوردگی را نسبت به دیگر انواع فولادهای ضد زنگ دارند. به طور کلی فولادهای ضد زنگ آستنیتی غیرمغناطیسی هستند و با استفاده از عملیات حرارتی سخت نمیشوند؛ اما میتوان با عملیات کار سرد یا cold working به میزان قابل توجهی سختی یا استحکام آنها را بالا برد.
فولاد ضد زنگ آستنیتی بیشترین قابلیت جوشکاری را در میان انواع دیگر فولاد ضد زنگ دارند و میتوانند به سه گروه تقسیم شوند:
- کروم- نیکل معمولی (رایج) یا سری ۳۰۰
- منگنز- کروم- نیکل- ازت یا سری ۲۰۰
- آلیاژهای ویژه
از جمله کاربردهای این نوع از فولاد زنگ نزن میتوان به موارد زیر اشاره کرد:
دیگ بخار، صنعت هوانوردی، قطعات الکترونیکی، تجهیزات راهآهن، مخازن شیمیایی، سیستمهای گرمایشی، تجهیزات کوره، مبدلهای حرارتی، لوله، اجاق گاز، سینک ظرفشویی، سقف ساختمان، ناودانی، در و پنجره، و…
فولاد سختگردان رسوبی علاوه بر کروم و نیکل، به میزانی مس، تیتانیوم و مولیبدن نیز در خود دارد. این نوع از فولادهای ضد زنگ انعطافپذیری بالایی داشته و در برابر خوردگی نیز مقاوم هستند؛ همچنین از استحکام بالایی در دماهای بالا برخوردارند. این فولادها میتوانند با افزودن عناصری مانند مس، Niobium و آلومینیوم مقاومت خود را بسیار افزایش دهند. مقاومت در برابر خوردگی این نوع را میتوان با فولادهای آستنیتی استاندارد مانند ۳۰۴ مقایسه کرد. از جمله کاربردهای این نوع از استنلس استیل میتوان به استفاده از آنها در قطعات فضایی و هواپیما اشاره نمود.
مزیتهای فولاد ضد زنگ (زنگ نزن)
اکنون مصرف سالیانه آهن زنگ نزن بیش از ۲۰ میلیون تن میباشد اما تقاضای جهانی برای فولاد ضد زنگ، با سرعتی در حدود پنج درصد در سال در حال افزایش است. مزیتهای فولاد ضد زنگ را میتوان در مقایسه با فولادهای با کربن معمولی به دست آورد. اگرچه فولادهای ضد زنگ طیف وسیعی از خواص را دارند، به طور کلی در مقایسه با فولادهای معمولی دارای خواص زیر میباشند:
- مقاومت بیشتر در برابر خوردگی (تمام فولادهای ضد زنگ از آلیاژهای آهن هستند که دارای حداقل حدود ۱۰٫۵ درصد کروم میباشند. کروم موجود در آلیاژ یک لایه اکسید محافظ خود ترمیمکننده را تشکیل میدهد. این لایه اکسید باعث همان مقاومت در برابر خوردگی فولاد ضد زنگ میشود. حتی اگر این لایه از بین برود، میتواند خود را ترمیم کرده و همچنان در برابر خوردگی مقاوم بماند.)
- سختی یا کرایوژنیک بالاتر (مقاومت کرایوژنیک با شکلپذیری یا چقرمگی در دماهای زیر صفر اندازهگیری میشود. در دمای کرایوژنیک، مقاومت کششی فولادهای ضد زنگ آستینی به طور قابل ملاحظهای بالاتر از دمای محیط است.)
- مقاومت گرمایی بالاتر
- انعطافپذیری بیشتر
- استحکام و سختی بالاتر
- ظاهری جذابتر (از مات تا براق، قابلیت رنگآمیزی و ایجاد نقش برجسته روی آن)
- نگهداری آسانتر
- عدم نیاز به پوشش محافظ (در مقابل فولادهای با کربن معمولی با پوششهایی مانند گالوانیزه در برابر خوردگی محافظت میشوند.)
محصولاتی که با استیل ضد زنگ ساخته شده به راحتی تمیز میشوند و میتوان از مواد شوینده معمولی مانند صابون برای تمیز کردن آنها استفاده کرد. فولاد ضد زنگ به طور کامل در زمینههایی مانند دکوراسیون منزل و لوازم آشپزی که نیاز به شستشوی مکرر دارند قابل استفاده هستند و پاسخگویی کاملی دارند.
فولاد ضد زنگ نوعی ماده سبز است به این معنی که قابلیت بازیافت دارد و به محیط زیست آسیب نمیرساند. در بخش ساخت و ساز قابلیت بازیافت آن نزدیک به ۱۰۰ درصد است. این ویژگی باعث میشود که فولاد ضد زنگ برای ساخت سازههایی که در معرض هوای نامطلوب قرار دارند، مناسب باشد.
از جمله محصولات استنلس استیلی که آهن آنلاین ارائه میکند میتوان به این موارد اشاره نمود:
- ورق استیل
- لوله استیل
- پروفیل استیل
برای کسب اطلاع از میتوانید به لینک فوق مراجعه کنید و قیمت بهروز این مقطع فولادی را مشاهده کنید.
کاربردهای فولاد ضد زنگ
فولاد ضدزنگ به تنهایی نام یک نوع فولاد نیست؛ بلکه نام خانوادهای از فولادهای مقاوم در برابر خوردگی است. این فولاد به دلیل مقاومت بالا در برابر خوردگی و دوامیک ساختمان در که با فولاد زنگنزن ساخته شدهاست.
و سایر فازهای آلیاژی آهن-کربن |
رده ها و کلاسهای مختلف |
سایر مواد پایه-آهنی |
فولادهای زنگنزن به دلیل ویژگی خود میتوانند مقاومت بسیار خوبی دربرابر خوردگی از خود نشان دهند. این فولادها به دلیل شکل گرفتن یک لایه غیرفعال بر روی سطحشان که به شدت به ماده زیرین پیوند خوردهاست و از تماس بیشتر ماده به محیط اطراف جلوگیری میکند، چنین ویژگیای دارند. برای اینکه این پدیده غیرفعالسازی بهطور پایدار در فولاد اتفاق بیفتد نیاز است که حداقل ۱۰٫۵ درصد از ماده را کروم تشکیل دهد. با داشتن چنین سطحی از کروم حتی اگر خراشی بر روی سطح فولاد ایجاد شود و این لایه از میان برود فولاد میتواند خودش را ترمیم کند و اگر گرید به درستی برای محیط کاری انتخاب شده باشد این لایه غیرفعال دوباره شکل میگیرد. در غیراینصورت شکست غیرفعالی رخ میدهد و فولاد زنگنزن، زنگزده و خورده میشود.
فولادهای زنگنزن به خاطر مقاومت دربرابر خوردگی خود بسیار مورد توجه هستند که این ویژگی با افزایش میزان کروم افزایش مییابد. افزودن عنصر باعث افزایش مقاومت به خوردگی فولادهای زنگنزن در مقابل اسیدهای کاهنده و دربرابر خوردگی در محلولهای کلرایدی میشود. به همین دلیل، انواع مختلفی از فولاد زنگنزن با میزان مختلف کروم و مولیبدن برای مطابقت با محیطی که آلیاژ باید تحمل کند وجود دارد. مقاومت فولاد زنگنزن به خوردگی و زنگزدگی، نیاز به نگهداری کم و درخشش بالا، آن را تبدیل به یک ماده ایدهآل برای بسیاری از کاربردها که در آن هم نیاز به استحکام بالا و هم نیاز به مقاومت به خوردگی بالا است کردهاست.
گنبد در شهر از فولاد زنگنزن ساخته شدهاست تا دربرابر زنگزدگی در شرایط مختلف آبوهوایی مقاوم باشد.
فولاد زنگنزن به شکل ، صفحه، میله، و ساخته میشود و در ، ، ، بزرگ؛ ، تجهیزات صنعتی (برای مثال در ، ، )؛ و مخازن ذخیره آب و مخازن و محصولات غذایی (به عنوان مثال، تانکرهای مواد شیمیایی و تانکرهای کامیونی) استفاده گردد.
مقاومت خوب دربرابر خوردگی، راحتی تمیز و استریل نمودن با و عدم نیاز به پوشش دادن سطحی، استفاده از فولاد زنگنزن را در آشپزخانههای تجاری و صنعتی متداول کردهاست.
جهانی فولاد زنگنزن در سال ۲۰۱۹ معادل ۱۱۱٫۴ میلیارد دلار ارزیابی شده و پیشبینی میشود تا سال ۲۰۲۷ با ۶٫۳٪ این مقدار به ۱۸۲٫۱ میلیارد دلار برسد. بزرگترین تولیدکننده و مصرفکننده محصولات فولاد زنگنزن در سطح جهان است که دلیل آن صنایع روبهرشدی مانند ، و کالاهای مصرفی است. شرکتهای اصلی تولیدکننده فولاد زنگنزن در جهان عبارتند از: ، ، ، ، ، ، ، ، و .
اختراع فولاد زنگنزن در پی اکتشافات مختلفی اتفاق افتاد. نخستین واقعه معرفی عنصر توسط به در سال ۱۷۸۹ بود. در اوایل دهه ۱۸۰۰، جیمز استودارت، و مقاومت آلیاژهای آهن-کروم (“فولادهای کرومی”) را دربرابر مشاهده کردند. رابرت بونسن مقاومت کروم دربرابر اسیدهای قوی را کشف کرد. مقاومت دربرابر خوردگی آلیاژهای آهن-کروم احتمالاً نخستین بار در سال ۱۸۲۱ توسط ، که مقاومت آنها را دربرابر حمله برخی از اسیدها نشان داد و استفاده از آنها را در کارد و چنگال پیشنهاد کرد، تشخیص داده شد.
در دهه ۱۸۴۰، هم فولادسازان بریتانیا و هم فولادسازان آلمان در حال تولید فولاد کرومی (که به دلیل درصد کم کروم و درصد بالای کربن آن خاصیت مقاومت در برابر زنگ زدگی نداشت) بودند و کروپ این گروه از فولادهای کرومی را در دهه ۱۸۵۰ برای ساخت استفاده میکرد. در سال ۱۸۶۱، حق فولاد کرومی را اخذ کرد.
در اواخر دهه ۱۸۹۰، شیمیدان آلمانی فرایند (ترمیت) را برای تولید کروم عاری از کربن توسعه داد. میان سالهای ۱۹۰۴ و ۱۹۱۱، چندین محقق، به ویژه از فرانسه، آلیاژهایی ایجاد کردند که امروزه میتوان آنها را فولاد زنگنزن به حساب آورد.
از آزمایشگاه پژوهشی Brown-Firth در شفیلد انگلیس، در سال ۱۹۱۲ در پی کشف آلیاژی مقاوم دربرابر خوردگی برای لولههای اسلحه، آلیاژ فولاد زنگنزن مارتنزیتی را کشف و سپس صنعتی کرد. این کشف دو سال بعد در مقاله روزنامه ژانویه ۱۹۱۵ در اعلام شد.
برخی از پیشرفتهای عمده فناوری در دهه ۱۹۵۰ و ۱۹۶۰ که اجازه تولید تناژهای بالا با هزینه مقرون بهصرفه را داد، عبارتند از:
انواع فولادهای زنگنزن[]
دستهبندی انواع فولادهای زنگنزن
پنج دسته اصلی از فولادهای زنگنزن وجود دارد که عمدتاً توسط (بلورین) آنها طبقهبندی میشوند:
ساختار آستنیتی فولاد زنگنزن AISI 304
فولادهای زنگنزن آستنیتی[]
فولادهای زنگنزن آستنیتی را میتوان به دو زیرگروه سری ۲۰۰ و سری ۳۰۰ نیز تقسیم کرد:
سری ۲۰۰[]
نزدیک به ۵۰ سال است که تلاشهایی برای جایگزینی نیکل موجود در فولادهای زنگنزن آستنیتی با منگنز صورت میگیرد. هدف این است که نوسانات قیمت نیکل بر روی قیمت نهایی فولاد زنگنزن از میان برده شود. نتیجه این تلاشها فولادهای زنگنزن سری ۲۰۰ بودهاست. این سری از فولادها دارای نیتروژن اضافی هستند تا فاز آستنیتی را پایدارتر کرده و بتوان خواص استحکام بالای مورد نیاز برخی کاربردها را تأمین کرد. از نیز برای افزایش پایداری فاز آستنیتی و همچنین افزایش خواص کارسرد در این سری فولادها استفاده میگردد.
استفاده از نیتروژن باعث شده که سری ۲۰۰ نسبت به سری ۳۰۰ نزدیک به ۵۰٪ بیشتر باشد اما از طرفی به دلیل میزان نیکل کمتر مقاومت به خوردگی بالایی ندارند. استفاده از این فولادها در و تا انتهای قرن اخیر بسیار محدود بودهاست.
سری ۳۰۰[]
فولادهای زنگنزن سری ۳۰۰ فولادهای آلیاژ کروم-نیکل هستند، که تقریباً همه ریزساختار آستنیتی آن به دلیل وجود نیکل میباشد. در برخی گریدهای آلیاژ بالا برای کاهش میزان نیکل مورد نیاز از استفاده میشود. فولادهای سری ۳۰۰ بزرگترین گروه و پرکاربردترین فولادهای زنگنزن مورد استفاده هستند. معروفترین گرید آن است که با نام فولاد ۱۸/۸ یا ۱۸/۱۰ نیز شناخته میشود که در آن ۱۸٪ کروم و ۸ یا ۱۰٪ نیکل استفاده میشود. دومین فولاد زنگنزن آستنیتی پرکاربرد فولاد ۳۱۶ میباشد. افزودن ۲٪ به آن باعث شده که این فولاد مقاومت به خوردگی دربرابر اسید و مقاومت به خوردگی ناحیهای توسط یونهای کلر بیشتری از خود نشان دهد.
فولادهای زنگنزن آهنی (Ferritic)[]
فولاد زنگنزن آهنی دارای یک ریزساختار فریتی مانند فولاد کربنی است که یک مکعبی مرکز-بدنی (body-centered cubic) محسوب میشود و دارای ۱۰٫۵ تا ۲۷ درصد کروم و مقدار بسیار کمی نیکل یا بدون نیکل است. این ریزساختار به علت اضافه شدن کروم، در همه درجه حرارتها وجود دارد و مانند فولاد ضدزنگ آستنیتی با عملیات حرارتی سختکاری نمیشود. مانند فولاد ضدزنگ آستنیتی آنها را نیز با نمیتوان تقویت کرد. این فولادها مانند فولاد کربنی مغناطیسی هستند.
فولادهای زنگنزن فریتی معمولاً خود به ۴ زیر-خانواده طبقهبندی میشوند:
- گروه ۱ که دارای ۱۰ تا ۱۴ درصد کروم و عدد معادل مقاومت به حفره دار شدن (PREN, Pitting resistance Equivalent Number = %Cr + 3.3 %Mo+16 %N) حدود ۱۰ است، در شرایط غیر سخت یا زمانی که مقداری خوردگی سطحی قابل قبول است استفاده میشود. گریدهای معمول (EN 1.4003) AISI 403 و AISI 409Cb (EN A/4601) است که در لولههای اگزوز خودروها استفاده میشود.
- گروه ۲ که دارای ۱۴ تا ۱۸ درصد کروم و با حدود ۱۶ است. معروفترین گرید آن AISI 430 (EN 1.4017) است. این گرید برای جوشکاری مناسب نیست، زیرا رشد دانه در (HAZ) جوش موجب شکنندگی میشود.
- گروه ۳ بسیار شبیه به گروه ۲ است، اما افزودن Nb, Ti و/یا Zr در مقادیر کم، تهنشینی کاربید را افزایش میدهد که به نوبه خود سبب جلوگیری از رشد دانهها و شکنندگی جوشها میشود؛ بنابراین آنها بدون هیچ مشکل خاصی قابل جوشکاری هستند.
- گروه ۴ گریدهای این گروه را میتوان «فوق آهنی» نامید که دارای مقادیر بیشتری Mo، و/یا Cr میباشد. عدد PREN آنها بالای ۱۸ است، که آنها را برابر یا بهتر از (EN 1.4301) AISI 304 میکند. شناخته شدهترین گرید این خانواده AISI 434 و ۴۴۴ (به ترتیب EN 1.4113 و EN 1.4521) است.
ساختار مارتنزیتی فولاد AISI 4140
فولاد زنگنزن مارتنزیتی[]
فولاد زنگنزن مارتنزیتی طیف وسیعی از خواص را ارائه میدهد و به عنوان فولاد زنگنزن مهندسی، فولاد زنگنزن ابزاری و فولاد مقاوم دربرابر خزش استفاده میشود.
آنها به ۴ دسته تقسیم میشوند (با مقداری همپوشانی):
- گریدهای آهن-کروم-کربن: این دسته نخستین گرید استفاده شده بودند و هنوز هم بهطور گسترده در کاربردهای مهندسی و مقاوم دربرابر سایش استفاده میشوند.
- گریدهای آهن-کروم-نیکل-کربن: در این گریدها، مقداری از کربن با نیکل جایگزین شدهاست. این دسته دارای سختی و مقاومت به خوردگی بالاتری هستند.
- گریدهای پیرسختکاری شونده: گرید EN 1.4542 (که با نام PH 17-4 نیز شناخته میشود)، شناخته شدهترین گرید، قابلیت سخت شدن مارتنزیتی و پیرسختکاری را هردو باهم دارد. این فولاد میتواند استحکام بالا و خوب را به دست آورد و در صنایع هوافضا و دیگر صنایع کاربرد دارد.
- گرید مقاوم دربرابر خزش: افزودن مقدار کمی ، ، و استحکام و مقاومت خزش را تا حدود ۶۵۰ افزایش میدهد.
فولاد زنگنزن دوپلکس[]
فولاد زنگنزن دوپلکس دارای میکرو ساختار ترکیبی آستنیتی و فریتی است که هدف آن معمولاً تولید ترکیب ۵۰/۵۰ است، اگر چه در آلیاژهای تجاری این نسبت میتواند ۴۰/۶۰ باشد. آنها با کروم بالا (۱۹–۳۲ درصد) و مولیبدن (تا ۵ درصد) و درصد نیکل پایینتر از فولاد ضدزنگ آستنیتی مشخص میشوند. فولاد ضدزنگ دوپلکس در مقایسه با فولاد ضدزنگ آستنیتی تقریباً دو برابر استحکام دارد. میکرو ساختار ترکیبی آنها مقاومت به ترک ناشی از خوردگی توسط کلراید بیشتری نسبت به فولاد ضدزنگ آستنیتی گونه ۳۰۴ و ۳۱۶ فراهم میکند. خواص فولاد زنگنزن دوپلکس با مقادیر آلیاژ پایینتر از مقادیر فولادهای گرید فوق-آستنیتی با خواص آن مشابه است و استفاده از آن برای بسیاری از کاربردهای مهندسی مقرون به صرفهتر است. گریدهای فولاد دوپلکس بر اساس مقدار آلیاژ و مقاومت به خوردگی آنها در گروههای مختلفی تقسیمبندی میشوند.
فولادهای زنگنزن رسوب سخت شونده[]
فولادهای زنگنزن رسوب سخت شونده مقاومت به خوردگی در حدود فولادهای آستنیتی دارند، اما میتوان آنها را توسط فرایند سختکاری رسوبی (که سختکاری سنی یا سختکاری ذره ای نیز نامیده میشود) سختکاری کرد. معروفترین گرید آن PH 17-4 است که تقریباً ۱۷ درصد کروم و ۴ درصد نیکل دارد.
کاربرد فولادهای زنگنزن[]
فولادهای زنگنزن آستنیتی[]
راحتی تمیزکاری، زیبایی، مقاومت به زنگزدگی و بسیاری خواص دیگر استفاده از فولادهای زنگنزن را در ساخت وسایل آشپزخانه محبوب کردهاست.
اصلیترین کاربرد آنها در مخازن ذخیره و بهداشتی و بیمارستانی میباشد. همچنین این دسته از فولادهای زنگنزن متریال استاندارد در ساخت تجهیزات شیمیایی و قاشق و چنگال و لوازم آشپزخانه میباشد.
۳۰۴ و 304L[]
فولاد ۳۰۴ متداولترین فولاد زنگنزن مورد استفاده است. از این فولاد برای کاربردهای خانگی و صنعتی مانند تجهیزات حمل مواد غذایی و فرآوری مواد غذایی، پیچها، اجزا و قطعات ماشینآلات استفاده میشود. مقاومت خوب دربرابر خوردگی اتمسفریک و از ویژگیهای این فولاد است. گونه کم کربن این فولاد یعنی 304L در حالت بیشینه تنها دارای ۰٫۰۳٪ کربن است که باعث میشود از حساس شدن فولاد (رسوب کاربید در مرزِ دانهها) در هنگام جوشکاری جلوگیری گردد و به همین دلیل اگر نیاز به جوشکاری باشد باید از گونه 304L استفاده گردد.
۳۱۶ و 316L[]
بهتر از فولاد ۳۰۴ و ۳۲۱ و مقاومت به خوردگی بهتری نسبت به عواملی مانند در دماهای بالا و محلولهای ملایم .
یکی دیگر از کاربرد های فولاد ۳۱۶،استفاده در است،البته که برند های لوکس نوع ساخت ویژه ای برای ساعت خود دارند.ولی در بیشتر ساعت های روزمره شاهد فولاد ۳۱۶ هستیم.
به دلیل مقاومت بالایی که استیل 316 در برابر خوردگی دارد، از آن در محیطهای مستعد خوردگی، همچون محیطهای دریایی و اسکلهها که از رطوبت و شوری بالایی برخوردار است، استفاده میشود، و این باعث شده که این فلز به عنوان بهترین استیل دریایی شناخته شود.
همچنین استیل گرید 316 بعد از نوع 304 به عنوان پرکاربردترین نوع استنلس استیل محسوب میشود.
۳۲۱ و ۳۴۷[]
میتوان از آنها در جاهایی استفاده کرد که عملیات حرارتی محلول پس از انجام جوشکاری امکانپذیر نیست، مانند لولههای اصلی بخار، لولههای سوپرهیترهای بخار و سامانههای تخلیه دود موتورهای پیستونی و که در دماهای کاری میان ۴۲۵ تا ۸۵۰ درجه سلسیوس کار میکنند.
۳۰۴H[]
گونهای از فولاد ۳۰۴ است که مقاومت به بالایی دارد و حداقل میزان کربن آن برای دماهای کاری تا ۸۰۰ درجه سلسیوس هوای خشک تنظیم و استانداردسازی شدهاست.
۴۸۲۸[]
۳۰۹S و ۳۱۰S[]
فولادهای زنگنزن آهنی (Ferritic)[]
فولادهای ۱۱٪ کروم در ساخت اگزوز خودروها استفاده میشود. گریدهای ۱۷٪ کروم آن برای ساخت تجهیزات خانگی کاربرد دارد. گریدهای ۲۹٪ کروم آن مقاومت بسیار بالایی به خوردگی دارد و در آبهای شور دریا کاربرد دارد.
۴۰۹[]
به دلیل راحتی در دسترس بودن و خواص ساخت و شکل دهی خوب آن منجمله جوشکاری راحت، از این فولاد بهطور گستردهای استفاده میشود. از کاربردهای دما بالای شناخته شده آن استفاده در سامانههای اگزوز خودروها است که در آن دمای فلز محفظه مبدل کاتالیتیک بیشتر از ۵۵۰ درجه سلسیوس است. از این فولاد همچنین در کانالهای اگزوز و صداخفهکنهای توربینهای گاز (Silencer) استفاده میشود.
۴۳۰ و ۴۳۹[]
برای مبدلهای حرارتی، تانکرهای آب گرم، کندانسورها و اجزای کورهها استفاده میشود.
۴۴۶[]
در اجاقهای صنعتی، دمندهها، سامانههای اگزوز، اجزای کورهها، جعبههای بازپخت و (پیرومترها) استفاده میشود.
فولادهای مارتنزیتی[]
ساخته شده از فولاد زنگنزن
مانند بسیاری از فولادهای ساده کربنی این فولادها در حالت و –که سختی مناسبی دارند- استفاده میشوند. بستگی به گرید مورد استفاده از این دسته فولادها برای ساخت تجهیزات آشپزخانه و لوازم جراحی استفاده میشود.
۴۱۰[]
گونهای فولاد کاربرد عمومی است که برای بخار، شفت ، (Bolts) و اجزای مختلفی که نیاز به مقاومت خوردگی و استحکام متوسط در دماهای کاری تا ۵۰۰ درجه سلسیوس دارند.
فولاد زنگنزن دوپلکس[]
مقاومت به خوردگی[]
فولادهای زنگنزن (ردیف پایین) تحمل بیشتری در مقابل خوردگی نسبت به آلیاژهای مس-نیکل (ردیف وسط) و آلیاژهای آلومینیوم-برنز (ردیف بالا) در آب-نمک از خود نشان میدهند.
فولاد زنگنزن برخلاف وقتی که در معرض محیطهای مرطوب قرار میگیرد دچار خوردگی یکنواخت نمیشود. فولادهای کربنی محافظت نشده در هنگام ترکیب با هوا و به راحتی زنگ میزنند. لایه سطحی (زنگ) متخلخل و شکننده است. از آنجایی که اکسید آهن حجم بزرگتری نسبت به فولاد اصلی را اشغال میکند، این لایه گسترش مییابد و تمایل به لایه برداری دارد و باعث حمله بیشتر به لایههای زیرین فولاد میشود. در عوض، فولادهای زنگنزن دارای کروم کافی برای هستند. این پدیده در صورت قرار گرفتن در معرض اکسیژن موجود در هوا یا آب، خود به خود اتفاق میافتد و باعث ایجاد یک لایه نازک از اکسید کروم خنثی روی سطح میشود. این لایه نازک غیرفعال با مسدود کردن مسیر اکسیژن به سطح فولاد از خوردگی آن جلوگیری میکند و باعث میشود که خوردگی به قسمت داخلی فلز نرسد. این لایه نازک در صورت خراشیده شدن یا از میان رفتن (به دلیل قرار گرفتن موقتی در شرایط شدیدتر از میزان حد تحمل خوردگی)، خود را تعمیر میکند.
مقاومت این لایه به خوردگی بستگی به ترکیب شیمیایی فولاد زنگنزن، به ویژه درصد کروم دارد.
خوردگی فولاد زنگنزن میتواند زمانی رخ دهد که درجه یا گرید آن برای محیط کاری مناسب نباشد.
معمولاً میان ۴ گونه خوردگی تفاوت در نظر میگیرند: یکنواخت، ناحیه ای، گالوانیک و SCC (ترک خوردگی ناشی از تنش).
خوردگی یکنواخت[]
این خوردگی تنها در فولادهای زنگنزن درحالت فعال رخ میدهد. به عبارتی زمانیکه روی فولاد لایه اکسید غیرفعال وجود نداشته باشد. دادههای مربوط به خوردگی یکنواخت در جداولی گردآوری میشود که واکنش فولادهای زنگنزن را در محیطهای اسیدی مختلف جمعآوری میکند. از جداول خوردگی برای انتخاب صحیح گریدهای فولادهای زنگنزن میتوان استفاده کرد.
خوردگی ناحیهای[]
چهار گونه خوردگی ناحیهای برای فولادهای زنگنزن در نظر میگیرند:
خوردگی حفره ای بر روی قسمتی از یک پل آهنی
(Pitting)
خوردگی شیاری در فولاد ۳۱۶
(Crevice Corrosion)
نمایش میکروسکوپی یک برش پرداخت و صیقل شدهٔ فولاد که مورد حملهٔ خوردگی بیندانهای قرار گرفتهاست.
حفرهحفره شدن (Pitting)[]
این گونه خوردگی تنها در نواحی کوچکی از فولاد رخ میدهد و باقی سطوح توسط لایه غیرفعال محافظت میشوند. در برخی نواحی لایه غیرفعال ممکن است از میان برود و اگر این لایه خودش را ترمیم نکند خوردگی رخ میدهد و ممکن است به یک سوراخ کامل ختم شود.
PREN= Cr+3.3(Mo+0.5W) +16N
که در آن Cr بیانگر کروم، Mo مولیبدن، W تنگستن و N نیتروژن بر حسب درصد جرمی میباشد.
خوردگی شکافی (Crevice Corrosion)[]
یا HAZ بر روی یک فولاد زنگ نزن در اطراف ناحیه با تغییر رنگ محسوس قابل مشاهده است. ترک ناشی از تنش و خوردگی در فولادUNS S31603 که در شرایط آزمایش تبخیر قطره در ۱۱۰ درجه سلسیوس و زمان ۵۰۰ ساعت ایجاد شدهاست. حداکثر تنش اعمال شده برابر نصف تنش تسلیم ماده (۱۳۹ مگاپاسکال) و محیط کلرایدی اعمال شده آن آب دریای مصنوعی است ( ۸٫۲)
ترک ناشی از تنش و خوردگی فرایندی است که در آن تنشهای مکانیکی ناشی از بارگذاری و محیط خورنده بهطور همزمان باعث شکل گرفتن ترکهایی در جسم میشوند. این ترکها ممکن است پس از مدت زیادی قرار گرفتن در معرض سیال خورنده شکل بگیرند ولی با سرعت زیاد رشد کنند و باعث شکست ناگهانی قطعه شوند. فولادهای فریتی در مقابل این پدیده بسیار مقاوماند.
خوردگی دما بالا[]
اسیدها[]
محلولهای اسیدی را میتوان به دو دسته کلی تقسیم کرد: اسیدهای کاهنده مانند: و رقیق و اسیدهای اکساینده مانند: و اسید سولفوریک غلیظ. افزایش درصد کروم و مولیبدن باعث افزایش مقاومت به اسیدهای کاهنده میشود، در حالیکه افزایش درصد کروم و سیلیسیم مقاومت بیشتری به اسیدهای اکساینده میدهد.
غلیظ دارای ویژگی اکساینده ای مانند است و در نتیجه در این محیطها فولادهای زنگنزن سیلیسیم دار کاربرد دارند.
به هر گونه فولاد ضدزنگ آسیب میرساند و باید اجتناب شود.
همه انواع فولادهای زنگنزن دربرابر حمله و در مقاومت میکنند. در غلظتهای بالاتر و افزایش حمله رخ میدهد و فولاد ضدزنگ آلیاژ بالاتری باید انتخاب شود.
بازها[]
فولادهای ضدزنگ گونه ۳۰۴ و ۳۱۶ با هیچیک از بازهای ضعیف مانند ، حتی در غلظتهای بالا و در دماهای بالا، تحت تأثیر قرار نمیگیرند. این فولادها در معرض بازهای قوی مانند در غلظتهای بالا و درجه حرارت بالا، ممکن است به مقداری لایه برداری و ترک خوردگی دچار شوند.
افزایش درصد کروم و نیکل باعث افزایش مقاومت میشود.
خوردگی گالوانیک[]
خوردگی گالوانیک در اثر اختلاف در شاخص آندی پیچهایی از جنس فولاد زنگنزن و ورق فولادی گالوانیزه
الزامات طراحی پیچیده باعث ترکیب فلزات مختلف در کنار یکدیگر میشود. در شرایط خاصی، این استفاده از فلزات در تماس با یکدیگر میتواند باعث خوردگی یکی از فلزات مورد استفاده شود. به این پدیده، گفته میشود و در آن دو فلز مختلف یک جفت گالوانیک تشکیل میدهند. در اکثر کاربردهای عملی، فولاد زنگنزن پتانسیل خوردگی مثبت بیشتری دارد، در نتیجه احتمال خوردگی بیشتر در فلز جفت شده با آن میباشد.
مطالعات و پژوهش بسیار زیادی در زمینه رفتار و سازگاری ترکیبات مختلف در رابطه با خوردگی گالوانیک در شرایط مختلف انجام شدهاست که شامل فولاد زنگنزن نیز میباشد. استاندارد DIN 50919 یکی از منابعی است که برای مطالعه رفتار خوردگی گالوانیک ترکیبات مختلف موجود است.
در حالت کلی میتوان گفت که میان گریدهای مختلف فولادهای زنگنزن در تماس با یکدیگر خوردگی گالوانیک رخ نمیدهد چرا که پتانسیل خوردگی آزاد هر دو جفت یکسان است.
انواع کیفیت و پرداخت سطح[]
سطح فولاد زنگنزن نشده، پرداخت نورد
برای رسیدن به کیفیت و حد پرداخت استاندارد بهطور مستقیم میتوان از غلتکها و سایندههای مکانیکی استفاده کرد. نخست فولاد برای رسیدن به ضخامت مورد نظر از داخل نورد عبور میکند و سپس فرایند برای رسیدن به خواص مکانیکی مطلوب انجام میشود. اکسیدی که روی سطح تشکیل میشود (رسوب نورد) با حذف میشود و یک بر روی سطح ایجاد میشود. سپس میتوان پرداخت نهایی را برای رسیدن به زیبایی مورد نظر اعمال کرد:
گونه مسیر فرایند و پرداخت سطح ورق، پلیت و تسمه(پانویس ۱) مطابق با استاندارد اروپایی EN 10088-2:2005 (E) | ||||
نماد | گونه مسیر فرایند | پرداخت سطح | نکتهها | |
نورد گرم شده | 1U | نورد گرم شده، بدون عملیات حرارتی، بدون رسوب زدایی | پوشیده شده از رسوب ناشی از نورد | مناسب برای محصولاتی که قرار است فراوری بیشتری بر روی آنها انجام شود، مانند تسمهای که قرار است بعداً دوباره نورد شود |
1C | نورد گرم شده، عملیات حرارتی شده، بدون رسوب زدایی | پوشیده شده از رسوب ناشی از نورد | مناسب قطعاتی که قرار است در آینده ماشین کاری یا رسوب زدایی شود یا برای استفاده در کاربردهای مقاوم-به-گرما. | |
1E | نورد گرم شده، عملیات حرارتی شده، رسوب زدایی مکانیکی | عاری از رسوب | انتخاب گونه رسوب زدایی مکانیکی، برای مثال خشن یا ، به گرید فولاد و محصول بستگی دارد، و به اختیار سازنده واگذار میشود، مگر اینکه غیر آن توافق شود. | |
1D | نورد گرم شده، عملیات حرارتی شده، شده | عاری از رسوب | معمولا برای اکثر فولادهای زنگنزن انتخاب استاندارد است تا از مقاومت به خوردگی اطمینان حاصل شود؛ همچنین برای فراوری بیشتر یک انتخاب پرداخت متداول است. وجود خطوط سنگ زنی مجاز است. به صافی 2D یا 2B نیست. | |
نورد سرد شده | 2H | شده | روشن | جهت افزایش استحکام کارسرد شدهاست. |
2C | نورد سرد شده، عملیات حرارتی شده، رسوب زدایی نشده | صاف با رسوب ناشی از عملیات حرارتی | مناسب قطعاتی که قرار است رسوب زدایی شده یا در مراحل بعدی فراوری، ماشینکاری شوند یا برای کاربردهای دما-بالای خاص. | |
2E | نورد سرد شده، عملیات حرارتی شده، رسوب زدایی مکانیکی | زبر و کدر | معمولا بر روی فولادهایی که نسبت به اسیدشویی بسیار حساس هستند اعمال میشود. ممکن است اسیدشویی شوند. | |
2D | نورد سرد شده، عملیات حرارتی شده، اسیدشویی شده | صاف | ||
2B | نورد سرد شده، عملیات حرارتی شده، اسیدشویی شده، انجام شده (Skin-passed) | صاف تر از 2D | ||
2R | نورد سرد، شده (Bright-Annealed)(پانویس ۳) | صاف، سطح روشن، بازپخت شده | ||
2Q | نورد سرد شده، سختکاری و تمپر شده، فاقد رسوب | بدون رسوب | ||
پرداختهای مخصوص | 1G
یا 2G |
سنگ زنی شده(پانویس ۴) | پانویس ۵ را ببینید. | |
1J
یا 2J |
برس شده(پانویس ۴) یا پرداخت سطح کدر(پانویس ۴) | صافتر از سنگ خورده. پانویس ۵ را ببینید. | ||
1K
یا 2K |
پولیش ساتنی(پانویس ۴) | پانویس ۵ را ببینید. | ||
1P
یا 2P |
پولیش روشن | پانویس ۵ را ببینید. | ||
2F | نورد سرد شده، عملیات حرارتی شده، نورد پاس پوسته با غلتکهای خشن | سطح یکنواخت و مات و غیرآینه ای | ||
1M | طرح دار | طرح باید توافق شود، سطح صاف | ||
2M | ||||
2W | موج دار | طرح باید توافق شود | ||
2L | رنگ دار(پانویس ۴) | رنگ باید توافق شود | ||
1S
یا 2S |
پوشش دار(پانویس ۴) | برای مثال با قلع یا آلومینیوم پوشش دهی شدهاست | ||
پانویس ۱: همه فرایندها و همه پرداخت سطوح برای همه فولادها قابل اعمال نیستند.
پانویس ۲: عدد اول: ۱=نورد گرم، ۲=نورد سرد پانویس ۳:ممکن است نورد پاس-پوسته داشته باشد. پانویس ۴: تنها یک سطح، مگر اینکه در سفارش خرید توافق شده باشد. پانویس ۵: در هر شرح پرداخت سطح، ممکن است خواص سطح تفاوت داشته باشد، و الزامات دقیق تری باید میان خریدار و فروشنده توافق شود. (برای مثال درجه گریت ) |
فولاد زنگنزن در دماهای بالا[]
از فولادهای زنگنزن علاوه بر کاربردهای مقاوم دربرابر خوردگی رطوبتی، در محیطهای دما بالا که فولادهای کربنی و کم آلیاژ مقاومت به خوردگی یا استحکام مناسب ندارند نیز استفاده میشود.
در کاربردهای دمابالا معمولاً عوامل زیر مدنظر است:
- استحکام خزشی بالا (و/یا چقرمگی)
- مقاومت مناسب دربرابر اکسایش و همچنین خوردگی ناشی از دمای بالا
- ریزساختار پایدار
- مقاومت مناسب در مقابل خوردگی سایشی
نقش عناصر آلیاژی مختلف[]
- کروم: نقش کروم بیشتر در دماهای بالای ۵۰۰ درجه سلسیوس مشخص میشود. این عنصر باعث شکل گرفتن یک لایه اکسید غنی از کروم مقاوم بر روی سطح میشود که از رسیدن بیشتر اکسیژن به لایههای زیرین و در نتیجه زنگزدگی جلوگیری میکند.
- سیلیکون و آلومینیوم: نقش سیلیکون و مشابه نقش کروم است. اگر این عناصر به اندازه کافی در سطح موجود باشند میتوانند باعث شکل گرفتن لایههای SiO2 و Al2O3 در سطح شوند. برای شکل گرفتن بیشتر این لایهها مقدار کمی از عناصر فلزی کمیاب کره زمین مانند یا میتواند بسیار کمککننده باشد.
- نیکل: نیکل باعث افزایش چقرمگی، استحکام دمابالا و افزایش مقاومت در مقابل کربوریزه شدن و نیتریده شدن میشود.
- نیتروژن و کربن: باعث افزایش استحکام خزش میشوند.
- مولیبدن: باعث افزایش استحکام ترکیدگی ناشی از خزش میشود.
- تیتانیوم: درصد کمی تیتانیوم، در حدود ۰٫۳ تا ۰٫۷ درصد، میتواند در فولادهای آستنیتی باعث افزایش استحکام شود. در مورد نیوبیوم نیز این مورد صادق است.
- بور: در غلظتهای بسیار پایین، در حدود ۰٫۰۰۲ درصد باعث افزایش استحکام ترکیدگی ناشی از خزش میشود.
نقش ریزساختار به اندازه برای مقاومت در دماهای بالا چندان مهم نیست اما انتخاب صحیح آن نیز بی تأثیر نیست.
- فولادهای فریتی: برای اکثر فولادهای فریتی بیشینه دمای کاری ثابت ۲۵۰ درجه سلسیوس است چرا که این فولادها در دمای ۴۷۵ درجه سلسیوس دچار تردی میشوند. این نکته در مورد فولادهای زنگنزن کروم پایین ۱۰٫۵ تا ۱۲٫۵ درصد چندان مهم نیست و دما میتواند برخی اوقات به ۵۷۵ درجه سلسیوس نیز برسد. فولادهای زنگنزن با درصد آلیاژ بالا با درصد کروم ۲۳ تا ۲۷ درصد، در دماهای بالا مقاومت به خوردگی فوقالعاده ای از خود نشان میدهند. روتور توربینهای بخار از فولادهای زنگنزن مارتنزیتیک که مناسب برای دماهای بالا است ساخته میشود.
- فولادهای مارتنزیتی: در استاندارد EN 10088-1 و EN 10302 فولادهای زنگنزن مارتنزیتی در رده فولادهای مقاوم به خزش قرار گرفتهاند. با این حال به دلیل اینکه سطح کروم آنها آنچنان بالا نیست (حداکثر ۱۲٫۵٪) این فولادها جرو فولادهای مقاوم به گرما نیستند و تنها در جاهایی استفاده میشوند که نیاز به استحکام نهایی بالا، استحکام خزش و خستگی بالا، به علاوه مقاومت مناسب دربرابر خوردگی مد نظر باشد و بیشینه دما ۶۵۰ درجه سلسیوس باشد از آنها استفاده میشود. از فولادهای مارتنزیتی کم کربن و کربن-متوسط عموماً در توربینهای بخار، موتورهای جت و توربینهای گاز استفاده میشود.
- فولادهای آستنیتی: این فولادها در کنار آلیاژهای پایه-نیکل بهترین ترکیب مقاومت به خوردگی دما-بالا و استحکام مکانیکی دما-بالا را ارائه میدهند. در کاربردهای دما بالا، فولادهای زنگنزن آستنیتی دما-بالا اصلیترین انتخاب هستند.
- فولادهای دوپلکس: استحکام تسلیم آنها در محدوده ۵۵۰ تا ۶۹۰ مگاپاسکال در حالت بازپخت شدهاست که بهطور چشمگیری بیشتر از فولادهای فریتی و آستنیتی است. با این حال استفاده از این فولادها در دماهای بالا به دلیل تردی و افت شدید استحکام مکانیکی پیشنهاد نمیشود. بیشینه دمای کاری آنها معمولاً ۳۰۰ درجه سلسیوس است.
- فولادهای پیر سخت شده: این فولادها آلیاژهای کروم-نیکل هستند که در حالت سخت شده برای دماهای بالای ۴۲۵ درجه سلسیوس به دلیل افت شدید استحکام توصیه نمیشوند.
خواص مکانیکی در دمای بالا[]
استحکام مواد در دماهای بالا مانند استحکام آنها در دمای اتاق آزمایش نمیشود. در دماهای بالا مهمترین خواص مکانیی خزش و استحکام ترکیدگی (شکست یا پارگی ناگهانی) است. در دماهای معمولی و اتاق اگر یک قطعه زیر تنش تسلیم تحت کشش قرار بگیرد میتواند تا بینهایت بدون تغییر باقی بماند اما در دماهای بالا این قطعه آغاز به کش آمدن بدون وقفه میکند تا زمانی که از هم گسسته شود. سرعتی که فلز کش میآید را نرخ خزش مینامند. استحکام مکانیکی مواد در دماهای بالا را بر اساس خزش میسنجند یعنی توان ماده به مقاومت دربرابر تغییر شکل در طول زمان در یک دمای بالا.
فولاد زنگنزن در دماهای کرایوژنیک[]
در دماهای بسیار پایین فولادهای فریتی، مارتنزیتی و دوپلکس تمایل به ترد شدن پیدا میکنند، اما فولادهای آستنیتی استحکام خود را در دماهای پایین حفظ میکنند. فولادهای زنگنزن آستنیتی را میتوان «فولادهای » طبقهبندی کرد.
از میان فولادهای زنگنزن آستنیتی برخی به صورت گستردهای در تجهیزاتی که در دماهای زیر صفر کار میکنند استفاده میشوند. این دماها میتواند حتی به دمای جوش یعنی منفی ۲۶۹ درجه سلسیوس نیز برسد.
جستارهای وابسته[]
خوب یکی از مهمترین فلزات موجود در بازار است. اگرچه عرضه تجاری آن به بازار کمتر از یک قرن پیش اتفاق افتاده است، ولی به سرعت به یکی از مهمترین یا اساسیترین فلزات تبدیل شده و تقریبا هر صنعتی را از معماری و مهندسی گرفته تا علوم پزشکی شامل میشود.
از جمله کاربردهای این نوع از فولاد میتوان به موارد زیر اشاره کرد:
مصارف خانگی:
- کارد و چنگال، ظروف غذاخوری و سایر وسایل مشابه
- سینک ظرفشویی
- قابلمه و وسایل آشپزی
- اجاق گاز و باربیکیو
- مبلمان منزل
مصارف شهری:
- کیوسک تلفن
- نمای ساختمان
- آسانسور و پله برقی
- مترو و زیرساخت ایستگاههای آن
مصارف صنعتی:
- تجهیزات برای تولید مواد غذایی و دارویی
- قطعات موتور اتومبیل و هواپیما
- تانکرهای سوخت و شیمیایی
آلیاژهای مهم فولاد زنگ نزن
آلیاژ آهن–کروم این ماده اصلیترین عنصر فولادهای زنگ نزن به حساب میآید و به همین خاطر بررسی دیاگرام فازی و ساختارهای موجود در آن با توجه به درصد کروم از اهمیت بالایی برخوردار است.
آلیاژ آهن-کروم-نیکل-کربن (Fe-Cr-Ni-C) برای پایدارسازی فاز آستنیت استفاده میشود و از جمله فولادهای زنگ نزن است.
اثر عناصر آلیاژی بر فولاد زنگ نزن
همانطور که اشاره کردیم افزودن نیکل به آهن زنگ نزن مقاومت به خوردگی را در محیطهای خنثی و یا اکسیدکننده ضعیف بهبود میبخشد؛ اما قیمت آنها را نیز افزایش میدهد. همچنین مقدار کافی نیکل قابلیت انعطاف و شکلپذیری فولادها را بالا میبرد؛ زیرا امکان نگهداری آستنیت (FCC) در دمای محیط را میسر میسازد. افزایش مولیبدن به فولادهای زنگ نزن مقاومت به خوردگی را در حضور یونهای کلر افزایش میدهد، حال آنکه افزایش آلومینیوم مقاومت به پوسته شدن را در دماهای بالا بهبود میبخشد. کروم نیز برای افزایش مقاومت به خوردگی آن اضافه میشود.
برای تقویت فولاد زنگ نزن، عناصر آلیاژی مثل نیکل و کروم را به آن اضافه می کنند.
حتما بخوانید : آهن آنلاین
تفاوتهای فولاد ضد زنگ با فولاد گالوانیزه
اگرچه نمیتوان مقاومت و استحکام هر دوی این محصولات را انکار کرد ولی هرکدام جوانب منفی و مثبتی دارند که باعث میشود با توجه به نوع کاربرد، یکی را به گزینه مناسبتری جهت انتخاب تبدیل کند.
فولاد گالوانیزه با یک لایه نازک روی پوشش داده شده که به محافظت در برابر خوردگی کمک میکند. این محصول میتواند در برابر آب به خوبی مقاومت کند.
از سوی دیگر فولاد ضد زنگ با افزودن کروم به فولاد مذاب ساخته میشود. به دلیل استحکام و مقاومت آن در برابر زنگزدگی، این نوع از فولاد به عنوان فلز اصلی در ساخت و ساز مورد استفاده قرار میگیرد. در مقایسه با گالوانیزه، این محصول مقاومت بهتری در برابر اسید و باز داشته و گزینه مناسبی برای استفاده در محیطهای دریایی میباشد. اما نباید از فولاد زنگ نزن در اطراف استخر یا مکانهایی که در معرض کلر قرار دارند، قرار بگیرد؛ زیرا باعث از بین رفتن پوشش روی فولاد و زنگ زدن آن میشود.
هر دوی فولاد گالوانیزه و فولاد ضد زنگ از محافظت بسیار خوبی در برابر خوردگی برخوردارند؛ ولی مقاومت فولاد ضد زنگ بالاتر است. قیمت این دو محصول در مقایسه با هم بسیار متفاوتند؛ به گونهای که قیمت فولاد ضد زنگ چهار تا پنج برابر بیشتر از فولاد گالوانیزه میباشد. البته از طرفی دیگر، دسترسی به فولاد گالوانیزه راحتتر است.
رایجترین فولادهای زنگ نزن و تفاوتهای آنها
گرید ۳۰۴ از گروه آستنیتی رایجترین نوع فولاد ضد زنگ است. گرید ۳۱۶ نیز نوع متداول بعدی است که آن نیز از گروه آستینی میباشد و تقریبا همان خصوصیات فیزیکی و مکانیکی نوع ۳۰۴ را دارد. تفاوت این دو در این است که ۳۱۶ حدود دو یا سه درصد مولبیدن را در خود جای داده که این موضوع مقاومت در برابر خوردگی به خصوص در برابر کلریدها و سایر حلالهای صنعتی را افزایش میدهد.
به عبارت دیگر اساسیترین تفاوت بین ۳۰۴ و ۳۱۶ حضور مولبیدن در گرید ۳۱۶ میباشد. مولبیدن عنصری شیمیایی است که برای تقویت و سخت شدن فولاد استفاده میشود و عملکرد اصلی آن در گرید ۳۱۶ کمک به مبارزه در برابر خوردگی از کلرید است. ضد زنگ ۳۱۶ حاوی نیکل بیشتری نسبت به ۳۰۴ است؛ در حالی که ۳۰۴ حاوی کروم بیشتری نسبت به ۳۱۶ است. ۳۰۴ معمولا از ۱۸ درصد کروم و هشت درصد نیکل و استیل ۳۱۶ از ۱۶ درصد کروم و ۱۰ درصد نیکل و دو درصد مولبیدن تشکیل شده است.
هر دو فولاد از دوام بالایی برخوردارند و مقاومت بسیار خوبی در برابر خوردگی دارند. ۳۰۴ به دلیل مقاومت در برابر خوردگی و ارزانتر بودن پرکاربردترین و پر مصرفترین فولاد ضد زنگ در جهان است. دلیل گرانتر بودن استیل ۳۱۶ این است که مقاومت بالاتری در برابر خوردگی خصوصا در برابر کلریدها و محلولهای کلر دارد. این موضوع باعث میشود که ۳۱۶ در محیطهایی که در معرض نمک قرار دارند، مطلوبتر باشد.
دلیل اصلی استحکام و افزایش انعطاف فولاد زنگ نزن (ضدزنگ)
به طور کلی در فولاد ضد زنگ هرچه قدر میزان کروم بیشتر باشد، مقاومت آن در برابر خوردگی بیشتر میشود. علاوه بر آن با اضافه کردن عناصر دیگر خواص دیگری به این نوع از فولاد اضافه میشود که باعث انعطافپذیری و افزایش استحکام آن میشود.
در این مطلب تلاش کردیم تا توضیح جامعی در زمینه آهن زنگ نزن، کاربردها، مزیتها و انواع آنها را ارائه کنیم. اگر در این زمینه اطلاعاتی دارید، میتوانید آن را از طریق کامنت با ما و دیگر دوستان به اشتراک بگذارید.